Scroll to:
Assessment and Prediction of the Environmental Performance of Multi-Component Cements Using Statistical Analysis
https://doi.org/10.23947/2541-9129-2025-9-2-87-101
EDN: GJCTOU
Abstract
Introduction. The cement industry, a cornerstone of the construction sector, generates significant CO2 emissions (5–8% of global totals). Amid growing demands for sustainable development and green construction, the development of multi-component cements (MCCs) with clinker partially replaced by active mineral additives (slag, phosphogypsum) is critical for reducing environmental impact while enhancing properties such as sulfate resistance, strength, and deformation control. The core problem lies in the lack of systematic statistical approaches to optimize MCC compositions, which hinders achieving a balance between environmental sustainability and performance characteristics. Many studies on MCCs focus on strength and sulfate resistance, but rarely employ statistical methods for comprehensive composition optimization. Other works highlight the environmental benefits of MCCs, yet fail to propose systematic approaches for property prediction. The research gap stems from insufficient correlation analyses of the relationships between chemical composition and MCCs properties, as well as limited investigation into the impact of impurities (e.g., MgO, alkali oxides) on sulfate resistance, which restricts the development of versatile formulations. This study aims to develop statistical approaches for optimizing MCC compositions to enhance sulfate resistance, control self-stress and linear expansion, and reduce carbon footprint, thereby addressing the identified research gap. To achieve this, the following tasks are defined: conduct correlation analysis of the relationships between MCC chemical composition (SiO2, CaO, Al2O3, Fe2O3, SO3, etc.) and performance characteristics (sulfate resistance, self-stress, linear expansion) based on experimental data; evaluate the environmental efficiency of replacing clinker with active mineral additives (blast-furnace slag, phosphogypsum, calcium hydrogarnets) through carbon footprint calculations; identify key chemical components with the greatest influence on sulfate resistance and deformation properties, and provide optimization recommendations; investigate the impact of impurities in active additives (e.g., MgO, alkali oxides) on sulfate resistance and propose mitigation strategies; develop an adapted MCC component matrix to predict cement properties and ensure compliance with sustainable construction requirements. These objectives and tasks aim to bridge the scientific knowledge gap by integrating statistical methods into MCC development, enabling the creation of environmentally safe, high-performance building materials that meet modern standards.
Materials and Methods. The research is derived from the statistical assessment of experimental data presented in patent RU 2079458 C1 (authors Andreev V.V., Smirnova E.E.). Data on 8 formulations of multi-component cements were analyzed, including Portland cement clinker (Pikalevo), blast-furnace slags (Cherepovets, Magnitogorsk), electrothermosulfate slag (SPTI), calcium hydrogarnets (GGK-1, GGK-2), and phosphogypsum (Kingisepp). Relationships between the chemical makeup of constituents (SiO2, CaO, Al2O3, Fe2O3, SO3, etc.) and their performance characteristics (self-stress, linear expansion, and sulfate resistance), determined according to standard methods (GOST 310.1–76, GOST 310.4–81, TU 21–26–13–90), were examined. Correlation evaluation was used as the main method. Visualization of correlation matrices was carried out using heatmaps (Seaborn library in Python). Additionally, calculations of the economic and environmental efficiency of partially replacing clinker with the specified active admixtures were performed.
Results. The findings of the statistical review confirmed the significant impact of SiO2, Al2O3, and other elements on the performance attributes of cements. It was determined that the calculated replacement of 30% of clinker with SCMs allows for a mitigation of the carbon footprint by 25–40%. It was revealed that enhancing the SiO2 content in the cement formulation improves the sulfate resistance of the cement paste, and literature data suggest that thermal activation of slags boosts compressive strength by 12–15%, improving the degree of hydration of constituents and forming a denser cement matrix. Economic assessment demonstrated that clinker substitution with active supplements can decrease cement production costs by 10–15%.
Discussion and Conclusion. Correlation assessment substantiated the pivotal role of SiO₂ in bolstering the sulfate resistance of the cementitious material. It was found that the silicate blast-furnace admixture used (slag A) can diminish sulfate resistance, which is presumably explained by the presence of impurities such as MgO and alkali oxides. Evaluation of the basicity coefficient (B = (CaO + MgO + Al2O3) / SiO2) revealed that when B < 1, hydration processes deteriorate, resulting in the formation of weak gel structures necessitating compensation with pozzolanic supplements. Statistical calculations highlighted a strong positive correlation (r = 0.89) between sulfate resistance and linear expansion, validating the potential for regulating these features through the precise makeup of cement mixtures. Furthermore, calculations indicated that lowering the C3A content in clinker below 8% significantly enhances cement durability in aggressive environments. The developed statistical techniques can be used for refining formulations to create environmentally sustainable binders with improved performance characteristics. The need for further investigation to verify the models on a wider range of materials and under industrial conditions is acknowledged.
Keywords
For citations:
Smirnova E.E. Assessment and Prediction of the Environmental Performance of Multi-Component Cements Using Statistical Analysis. Safety of Technogenic and Natural Systems. 2025;(2):87-101. https://doi.org/10.23947/2541-9129-2025-9-2-87-101. EDN: GJCTOU
Introduction. MCCs play a key role in the modern construction industry due to their environmental and operational advantages. They can reduce the carbon footprint and improve the durability of structures, which makes their research extremely relevant in the context of increasing demands for sustainable construction. A review of recent publications shows considerable attention to the chemical composition of MCCs and their properties. In the works of A. Rashad (2023), the influence of steel fibers and calcium oxide on the properties of cements, including strength and resistance to aggressive media, is considered [1]. Geopolymers, being a promising alternative to cement due to their environmental friendliness and good compressive strength, have a significant disadvantage — brittleness, which results in low bending and tensile strength. To eliminate this, steel fibers of various shapes are introduced into the geopolymer matrix. In geopolymers based on slag or mixed binders, the introduction of fibers often leads to a decrease in water absorption and permeability, which is an important factor in increasing the durability of the material [2]. Studies by M. Rahman & M. Bassuoni (2014) [3], and M. Sakr & M. Bassuoni (2020) [4] emphasize the importance of preventing sulfate corrosion by optimizing cement composition. It also highlights the importance of reducing C3A content to increase the resistance of concrete to aggressive environments (Sivkov, 2015) [5]. M. Thomas et al. (2008) focus on delayed ettringite formation as a factor affecting durability [6]. I.P. Pavlova (2016) notes that plasticizing additives significantly affect strength characteristics and deformations of expanding cement systems. The choice of a plasticizer with the appropriate chemical structure significantly improves the characteristics of cement systems, contributing to their adaptation to the specific requirements of construction [7]. The work of T. Markiv et al. (2020) confirms the importance of studying the composition of cements in order to achieve optimal characteristics [8]. L. Srikakulam & V. Khed (2020) model the design of an engineering cement composite (ECC) with the addition of various mineral additives and fibers [9]. The article by Yum et al. (2020) evaluates the effect of calcium formate (CF) on strength development and microstructure of the CaO-activated crushed granular blast furnace slag (GGBFS) system [10]. Sanytsky et al. (2020) show that the introduction of nanomodifiers leads to significant improvements in cement properties [11].
L.D. Shakhova and D.E. Kucherov (2008) consider the practice of using MCCs in Germany. With the transition of cement industry to standardized production, it becomes necessary to choose cement based on its material and mineralogical compositions. Composite and multicomponent cements, including active additives and inert fillers, are of limited use in Russia. However, their use reduces the proportion of clinker and helps reduce CO2 emissions, as well as increases the strength and durability of concrete. The article also discusses the regulatory requirements and potential of new cements in various fields of construction [12].
M.N. Chomaeva (2019) analyzes the impact of cement industry on the environment and emphasizes the need to develop new types of cements with improved environmental performance. Problems with generation of toxic gases such as dioxins and cyanides require strict control over the composition of raw materials and the process temperature to prevent their formation and protect public health. The introduction of integrated technologies for dechromatization and waste disposal in the cement industry significantly reduces the level of heavy metals and other harmful impurities, which is an important step towards environmentally friendly production [13]. O.N. Khokhryakov's dissertation (2022) is devoted to the introduction of highly dispersed binders and the use of industrial waste in cement production to create new building materials that meet the requirements of modern construction. To improve the properties of cements, the author suggests using polycarboxylate superplasticizers, which increase fluidity and reduce water consumption, which makes it possible to achieve higher strength and durability of concrete structures [14]. Scientists emphasize that carbonate cements with low water consumption represent a promising and environmentally friendly alternative to traditional cements in Russia. They contribute to reducing carbon emissions and increasing the sustainability of building materials. Due to their ability to reduce water consumption and improve the plasticity of concrete mixtures, carbonate cements provide not only economic but also environmental efficiency, which meets the requirements of sustainable development [15]. In modern research on the mechanics of composites, special attention is paid to increasing the initial strength of cement materials through mechanical activation. The most noticeable results are achieved when activating a binary mixture of cement and sand, which significantly increases strength characteristics in the early stages of hardening [16]. The use of finely dispersed additives and superplasticizers allows achieving significant results in increasing the strength and durability of powder-activated concretes [17].
Despite significant advances in the study of MCCs, the problem of increasing their environmental sustainability while maintaining operational characteristics remains unresolved. One of the key tasks is to develop an adapted component matrix that would optimize the composition of cements for various operating conditions [18].
The relevance of the study is confirmed by modern requirements for reducing the carbon footprint in the construction industry and the need for environmentally friendly building materials [19]. In addition, international standards and programs require new approaches to the assessment and optimization of cement properties. According to S. Yang et al. (2023), the development of the construction industry in recent decades has been driven by increasing demands for optimal and efficient use of raw materials and energy resources. The need to follow a low-carbon development strategy is emphasized, which leads to an urgent need to increase the production of cements and concretes with reduced content of energy-intensive clinker and, as a result, to reduce CO2 emissions during their production. The article mentions specific initiatives such as the EU strategy for reducing greenhouse gas emissions and the Green Deal Program aimed at achieving climate neutrality by 2050, which indicates the global scale of the problem [20]. According to other authors, progress in construction and stricter requirements for safety and reliability of structures stimulate the development of new, highly efficient materials with increased strength and durability. At the same time, the importance of reducing the carbon footprint and improving the environmental safety of building materials is emphasized. It is noted that traditionally, a material such as ECC (engineered cementitious composite) is characterized by an increased cement content compared to conventional concrete, which not only causes technical problems (increased heat generation, shrinkage), but also negatively affects the cost and environmental impact of the material. As a solution to this problem, Sydor N., Marushchak U., Braichenko S., Rusyn B. propose partial replacement of Portland cement with industrial waste — fly ash [21]. The results of this study are of practical importance for manufacturers of building materials, as they allow us to develop new formulations of cements that enhance their stability and durability. They also contribute to solving global environmental problems related to reducing CO2 emissions. The aim of this work is to study the effect of MCCs on environmental performance and performance characteristics, as well as to develop approaches to optimizing their composition.
Materials and Methods. The objectives of the article were based on the analysis of current problems in the field of MCCs, including the need to reduce their carbon footprint, increase their durability and resistance to aggressive environments. Literature analysis made it possible to determine the current state of research, identify key problems and formulate aims of research.
The work used an integrated approach to determine the relationship between the chemical composition of cement components (SiO2, CaO, Al2O3, Fe2O3, SO3 etc.) and its performance characteristics (self-tension, linear expansion, sulfate resistance). The analysis was performed using the Pandas library and visualized using Seaborn heatmaps in Python. Python-based software was used for data analysis, which made it possible to efficiently process and visualize the results. Cement samples were obtained from a variety of sources, including Portland cement, blast furnace slag, and phosphogypsum, which provided a wide range of characteristics [22]. The data from the patent on the MCCs composition became the basis for a correlation analysis in order to assess the environmental effectiveness of cements and their predictive characteristics (Table 1).
Table 1
Chemical composition of components for cement mixtures (% by weight)
Component |
SiO2 |
CaO |
Al2O3 |
Fe2O3 FeO |
MgO |
Na2O/ Na2O3 |
K2O |
SO3/S |
TiO2 |
P2O5 |
MnO |
H2O |
ппп |
Others |
1. Portland cement clinker (Pikalevo) |
22.15 |
64.21 |
4.54 |
3.36 |
1.25 |
0.66 |
0.60 |
0.23 |
0.32 |
– |
– |
– |
2.08 |
– |
2. Blast furnace slag (Cherepovets, A) |
38.90 |
39.60 |
8.90 |
0.54 |
10.54 |
– |
– |
0.59 |
– |
– |
0.29 |
– |
– |
– |
3. Blast furnace slag (Magnitogorsk, B) |
37.48 |
40.87 |
11.00 |
0.25 |
7.67 |
– |
– |
0.93 |
0.51 |
– |
0.21 |
– |
– |
– |
4. Electrothermal sulfate slag (SPTI) |
41.25 |
46.83 |
2.63 |
2.61 |
2.47 |
– |
– |
0.35 |
– |
0.25 |
– |
– |
– |
1.16 |
5. Calcium hydrogarnet (GGK-1, Pikalevo)) |
0.1 1.58 |
37.72 38.31 |
24.60 24.91 |
0.16 0.16 |
0.70 0.72 |
5.75 5.84 |
– |
– |
– |
– |
– |
– |
24.96 29.49 |
– |
6. Calcium hydrogarnet (GGK-2, SPTI)) |
0.12 2.10 |
45.46 46.39 |
29.12 29.72 |
0.19 0.19 |
0.85 0.88 |
6.78 6.92 |
– |
– |
– |
– |
– |
– |
15.52 15.81 |
– |
7. Quartz sand (Volsk) |
98.55 |
0.58 |
0.64 |
0.13 |
– |
– |
– |
– |
– |
– |
– |
– |
– |
0.10 |
8. Phosphogypsum (Kingisepp) |
0.50 |
32.50 |
0.60 |
0.20 |
– |
– |
– |
44.30 |
– |
1.60 |
– |
19.40 |
– |
– |
In order to correctly interpret the results of statistical analysis and evaluate their representativeness and applicability, it was necessary to consider the methodology for obtaining the initial experimental data on which this analysis was based. These data were obtained during the work on patent RU 2079458 C1 and included the following stages of sample preparation and testing. The components were ground to a fineness of 10 of the residue on a 008 sieve, and then mixed in a laboratory mixer. As a result, eight MCC formulations were obtained and tested. Data on performance characteristics (self-tension, linear expansion, and sulfate resistance coefficient) was collected through standard laboratory tests of samples made from these eight compounds. Clearly identified components were used for their preparation: Portland cement clinker from the Pikalevsky association “Glinozem”, blast-furnace granular slags from Cherepovets and Magnitogorsk Metallurgical Plants, electrothermal sulfate slag from the SPTI (TU), two types of calcium hydrogarnet (GGK-1 from the Pikalevsky association “Glinozem” and GGK-2 from the SPTI (TU), quartz sand from the Volsky deposit and phosphogypsum from the Kingisepp association “Phosphorite”. Standard cement tests were performed in accordance with GOST 310.1.761, GOST 310.4.812 (extended in 2003), self-stress was determined according to TU 21–26–13–90 (in rings)3.
Results. Correlation analysis. The aim was to identify the relationships between the chemical composition of cement components and their properties, including self-stress, linear expansion, and sulfate resistance.
We used the code and got the correlation matrix (Fig. 1):
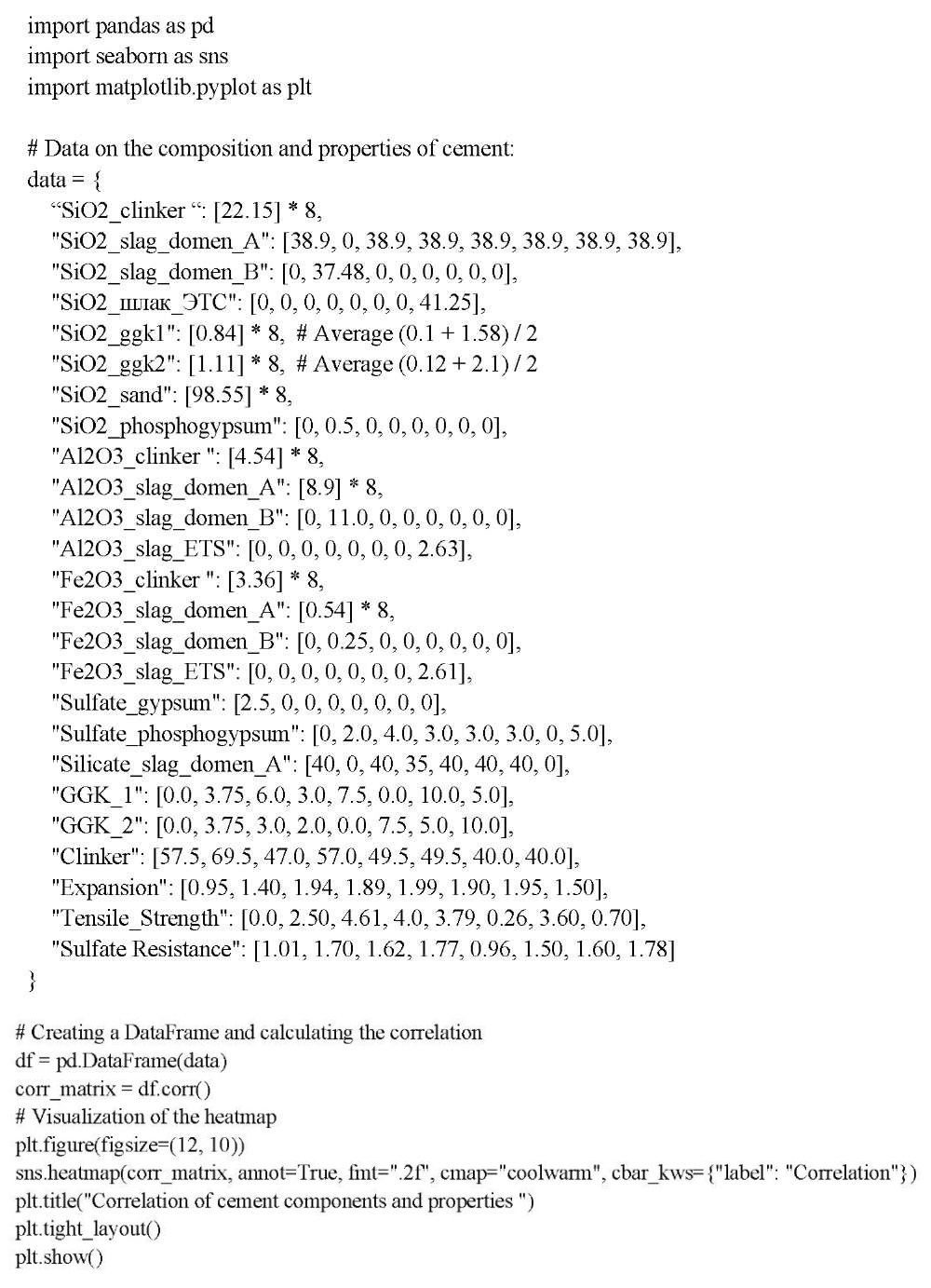
а)
b)
Fig. 1. Correlation matrix of chemical composition and properties of cement:
a — code (components: chemical compounds — SiO2, Al2O3, Fe2O3 from various sources
(clinker, blast furnace slag A and B, ETS slag, sand, phosphogypsum, GGK1, GGK2), additives: Sulfate_gypsum, Sulfate_phosphogypsum, Silicate_slag_domen_A, GGK_1, GGK_2, Clinker, properties:
Expansion, Tensile Strength, Sulfate Resistance;
b — heatmap (red (>0): positive correlation (an increase in one variable is associated with an increase in the other), blue (<0): negative correlation, white (≈0): no correlation. Some columns (for example, SiO2_clinker, SiO2_clinker) have constant values, which leads to zero correlation with other variables (NaN in the matrix is displayed as 0 or empty cells)
The correlation heatmap provides visual representation of strength and direction of linear relationships between various cement components (silicon oxides, aluminum oxides, iron oxides, calcium oxides, sulfates, and hydrogranates) and its properties (tensile strength, expansion, and sulfate resistance). The analysis of the map makes it possible to identify significant factors affecting the quality and behavior of the cement. Values close to +1.00 and –1.00 show a strong correlation. The map shows a negative correlation between SiO2_slag_domen_A and SiO2_slag_domen_B, which is expected, since both components are blast furnace slag with a high SiO2 content, and if the amount of one increases, the other decreases in order to maintain the total mass and chemical balance. In slag production, it is important to maintain an optimal ratio of oxides to achieve the desired properties. Slag stoichiometry should take into account a certain ratio of SiO2 and CaO to achieve good strength and sulfate resistance. When using different types of ore or melting temperatures, the SiO2 content has different variations. Less strong positive correlations are observed between different oxides within the same type of slag.
Clinker and oxides of Si, Al, Fe in blast furnace slags and phosphogypsum (r = 0.75). A positive correlation indicates their interaction in the cement structure. Various minerals such as C3S (tricalcium silicate), C2S (calcium disilicate), C3A (tricalcium aluminate) and C4AF (tetracalcium aluminoferrite) are formed during the firing of clinker raw materials (usually at temperatures around 1400–1500°C.). These minerals have different mechanical and chemical properties, and their formation depends on the content of SiO2, Al2O3, and FeO. Oxides contribute to the formation of stronger structural units in clinker, which is reflected in a positive correlation [23].
The GGK components (hydraulic additives) and Expansion, Tensile_Strength, Sulfate Resistance (r = 0.54 – 0.69). A moderate correlation indicates their statistical relationship. Changes in the clinker content directly alter the properties of the GGK components. This is important to control hydration and improve the early strength of the cement. The clinker content affects volume change of hydraulic additives. For example, certain minerals in clinker cause hydration, which leads to an increase in volume, which is associated with the formation of new phases or with changes in the structure of the material. The high content of clinker improves mechanical properties such as tensile strength due to the formation of durable minerals such as C3S and C2S, which provide good adhesion and strength in the hydrated state. Sulfate resistance depends on the ratio of oxides in clinker and the presence of certain phases such as C4A3S. An increase in the content of clinker rich in aluminates increases the resistance to sulfates, which is important for the long-term operation of concrete in aggressive conditions. Nevertheless, in cements containing active mineral additives, high sulfate resistance is ensured by a reduced content of C3A in clinker. Thus, in the standards of Great Britain, Germany and China, the content of C3A in high-sulfate-resistant cement is allowed equal to 3.5, 3.0 and 5.0, respectively. Optimizing the SiO2 content will help regulate the mechanical properties and prevent microcracks. An excessive increase in the proportion of SiO2 in clinker leads to deterioration in the sulfate resistance of cement [5].
A significant part of positive correlations is observed between the components associated with the same type of slag. The positive correlation between calcium oxide in blast furnace slag and sulfate resistance indicates sulfate resistance. Inclusion of CaO (3–5%) as an activator in the matrix reduces water absorption, overall porosity, increases wetting/drying, and acid resistance. CaO has a significant impact on compressive strength at an early age, compared to later age. The correlation between sulfates and sulfate resistance is expected to be weakly positive [1].
Tensile_Strength and Expansion (r = 0.67) suggests that the use of blast furnace slag contributes to the controlled expansion of cement.
Sulfate_phosphogypsum and Sulfate Resistance (r = 0.40). Phosphogypsum has a positive effect on sulfate resistance, confirming the importance of an alternative and environmentally friendly material capable of effectively suppressing linear deformations of cement mortars.
Silicate blast furnace additive (Silicate_slag_domen_A) and Sulfate Resistance (r = –0.51). The negative correlation contradicts the expected effect. Although the above slag composition looks typical, some components or impurities significantly reduce the resistance to sulfate corrosion. For example, the increased content of free magnesium oxide (MgO) or alkalis (Na2O, K2O) reduces the resistance to sulfates. Sulfate medium can cause the formation of thaumasite in the initial stages of the silicate-containing phase or delayed ettringite formation, which “explodes” concrete from the inside [3].
Clinker and Sulfate Resistance (r = –0.08). An increase in the proportion of clinker leads to a decrease in the ability to withstand sulfate attacks. The reason for this is low chemical resistance of clinker in a sulphate environment, which makes it necessary to replace it with alternative additives. Clinker, especially if it contains a high level of tricalcium aluminate (C3A), is less resistant to sulfate attacks. In this regard, it is advisable to use slag additives to improve sulfate resistance.
Clinker and Expansion (r = –0.45) indicate that clinker reduces the ability of cement to expand in a controlled manner, impairing mechanical stability. The high content of clinker leads to uncontrollable volume changes in concrete. Clinker minerals can affect hydration and the formation of hydrated phases. As a result, internal stress causes cracking [6].
Fe2O3 of blast furnace slag A and Expansion (r = –0.31). An increase in the Fe2O3 content reduces linear expansion due to the formation of more stable phases less susceptible to volume changes, which is useful for preventing cracking under aggressive conditions.
Thus, correlation analysis shows that minimizing clinker, replacing traditional additives with alternative materials (slags, phosphogypsum, etc.) and controlling the content of SiO2, Al2O3, and sulfate components are key strategies for improving the environmental safety of cement. This not only reduces the carbon footprint during production, but also increases the durability and sustainability of building materials, which is consistent with the principles of green construction.
Transition to an adapted matrix. The development of cement with predictable and improved characteristics requires a transition to an adapted matrix. It is necessary to accurately assess the key factors affecting the properties of cement and the needs for optimizing the composition in order to achieve the target characteristics. The requirement for sulphate resistance of cement, which must be at least 9 units for use in aggressive environments, is extremely relevant. This indicator, as can be seen from the analysis, has a strong correlation with the content of SiO2, Al2O3 and sulfate components, which emphasizes their priority importance in simplifying the matrix.
Another important consideration is the optimization of linear expansion. The data show that an increase in the SiO2 content of blast furnace slag and sand contributes to controlled expansion, which is critically important for preventing cracking in structures. The components that directly affect this indicator should be identified as the key ones. The transition to a simplified matrix will allow us to focus on the most important factors and develop a more accurate and practical model for predicting cement properties.
The updated code is provided below. After that, we obtain the correlation matrix (Fig. 2):
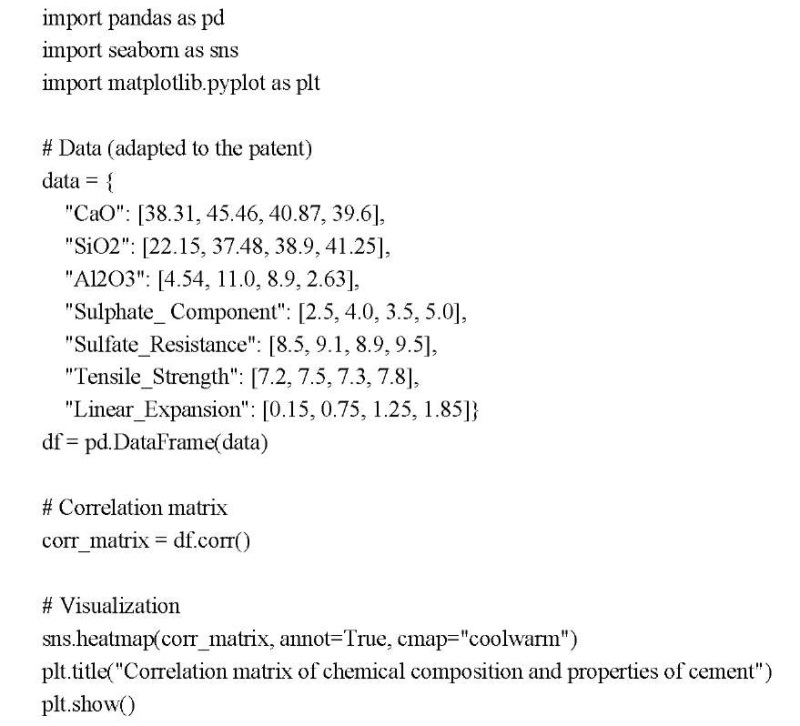
а)
b)
Fig. 2. Updated correlation matrix of chemical composition and properties of cement:
a — code (components: chemical compounds — CaO, SiO2, Al2O3, additive: Sulphate_Component, properties: Sulfate_Resistance, Tensile_Strength, Linear_Expansion);
b — heatmap (high correlation between CaO and Sulfate resistance indicates the effect of calcium on the resistance of cement to sulfates. SiO2 and Al2O3 have a weak correlation with each other if their content varies independently. Linear_Expansion and Tensile_Strength correlate with Sulphate_Component, reflecting the effect of additives on deformation properties)
Matrix analysis and conclusions:
- It is found that sulfate resistance of cements has a weakly positive correlation with the CaO content (r= 0.28). To increase it, you need to focus on other components (for example, SiO2 or Self_Tension) that show a stronger effect;
- Strong positive correlation between SiO2 content and sulfate resistance (0.87) indicates the need to optimize the proportion of SiO2 to increase environmental sustainability;
- Self-tension level strongly correlates with sulfate resistance (0.97), which confirms its importance for this property. Self-tension helps the material to cope with the chemical stresses caused by sulfates;
- Correlation (1.0) means that the Sulfate_Component (for example, Ca6Al2(SO4)3(OH)12*26H2O) and sulfate resistance change together;
- High positive correlation (0.89) between sulfate resistance and linear expansion in expanding MCCs is explained by the complex interaction of components, including additives, slags and hydrogarnets, which can simultaneously affect both properties, as well as controlled expansion in the early stages of hydration, potentially increasing sulfate resistance within certain limits[7].
- An increase in the silicon oxide content leads to an increase in linear expansion and vice versa (0.88). This indicates that SiO2 is the main component for controlling cement expansion [24]. Typically, the mass fraction of SiO2 in Portland cement is at least 25%4. To increase the sulfate resistance of cement, it is recommended to reduce the content of tricalcium aluminate (C3A) to no more than 8%5. Forecast: an adjustment of the SiO2 fraction by 10% will provide an increase in sulfate resistance by 8.7%, including the composition optimization (the introduction of a more active sulfate component — phosphogypsum or fluorogypsum).
Discussion and Conclusion. Regarding the representativeness and applicability of the conclusions. It is beyond argument that, the direct quantitative transfer of the results to all possible real production conditions requires caution. However, the use of standardized test methods and components from well-known industrial sources provides a certain basis for assessing the identified dependencies. Eight tested formulations represent variations of multicomponent systems that allow us to identify statistical trends.
When it comes to the applicability of conclusions beyond a specific context, qualitative and quantitative aspects should be distinguished. The conclusions about the key role of SiO2 in providing sulfate resistance, the effect of C3A content, the positive correlation between sulfate resistance and linear expansion, as well as the environmental and economic effects of replacing clinker with active additives are generally consistent with general scientific concepts and the results of other studies cited in the article [1][3][5][12]. These qualitative patterns are likely to have broader applicability. However, specific quantitative correlations and forecasts (for example, an increase in sulfate resistance by 1% SiO2) are strictly applicable to this studied system and require additional verification and adaptation to other types of cements, raw materials from other regions or other production conditions.
Regarding the limitations of the scale of application and the variability of slags, we can agree that the article does not sufficiently address the issues of scaling results to industrial conditions and the impact of differences in technological processes at different plants. However, the study focuses on analyzing laboratory-level data. It is recognized that the effectiveness of additives, in particular blast furnace slags (and their thermal activation, which is mentioned later in the discussion), can vary depending on their chemical composition, the presence of impurities (MgO, alkalis) and production conditions, which differ in different regions. The observed negative correlation for one type of slag may be related to these factors. Therefore, the applicability of the developed approaches on an industrial scale requires further research and adaptation, taking into account the specifics of a particular production and the raw materials used.
An unexpected negative correlation (r = –0.51) between silicate blast furnace additive (slag A, Cherepovets) and sulfate resistance has been identified and recognized above. As explanations, hypotheses are put forward about the influence of impurities in this particular slag, such as MgO or alkaline oxides, or about the possible formation of harmful phases such as thaumasite or delayed ettringite in the presence of sulfates. This phenomenon requires further, more in-depth research to clarify the exact mechanisms underlying it, which goes beyond the scope of the conducted correlation analysis.
Taking into account the limitations of the laboratory scale, the variability of raw materials and the need for further research on some points, it can be argued that the analysis nevertheless revealed statistically significant trends. The results of the correlation analysis showed complex relationships between the composition of MCCs and their properties. The importance of reducing the proportion of clinker to increase sulfate resistance and control linear expansion has been confirmed. Studies by A.S. Brykov (2014) [23] and A.M. Rashad (2023) [1] demonstrate that reducing the proportion of clinker by 30% and replacing it with activated additives (e.g. slags and phosphogypsum) leads to a 25–40% reduction in CO2 emissions. However, the optimal use of slag in concrete mixtures should be monitored. It makes up about 40% of the total binder content [25]. According to J. He et al. (2023), the production of AAS (alkali-activated slag) cement can reduce CO2 emissions by up to 78.1%, compared with conventional Portland cement, contributing to a reduction in environmental impact [26]. In the framework of this study, this is confirmed by calculations. The equation of environmental efficiency:
(1)
where Cbase — content of clinker in the basic composition (65%); Cmod — content of clinker in the modified composition (35%).
If the proportion of clinker is replaced by 30%, the reduction in CO2 emissions will be:
This indicator is consistent with data from the scientific literature and highlights the contribution of this study to environmentally friendly technologies.
Replacing clinker with additives reduces the cost of cement by introducing production waste, which corresponds to the conclusions of economic efficiency. The economic contribution can be calculated using the formula:
(2)
where C — volume of the component; P — unit cost.
For example, patent RU 2342337 C1 states that when adding 10% of the mineral additive by weight of clinker, the cost of cement decreases by about 8–10%, and when adding 20% — by 13–15% [27].
A strong correlation is found between the SiO2 content and sulfate resistance (r = 0.87), which opens up opportunities for optimizing the cement composition by regulating the proportion of silica. The indicator coincides with the data of S.V. Bastrygina and R.V. Konokhov (2022). According to their model, an increase in the proportion of SiO2 in the amount of 0.5–2.0 wt. % increases the strength of concrete by 15–40% [28]. The article by N.E. Dzhabbarova and U.F. Gasanova also claims that the addition of silica to cement in an amount of 10% increases the compressive and bending strength (by 50 and 16%, respectively), in an amount of 20% — leads to a maximum increase in strength
(72 and 18%) [29]. In our study, the calculations show that to achieve the required sulfate resistance (at least 9 units) at an initial value of 8.5, it will take:
(3)
where T = 9T = 9 (target sulfate resistance); Sbase = 8.5 (initial resistance); K = 0.5 (average increase in resistance by 1% SiO2).
Let us find the value of sulfate resistance:
This calculation is generally consistent with the literature data and highlights the role of SiO2 in the development of cements for aggressive environments.
Similarly, M.M. Rahman et al. (2014) emphasizes the importance of optimizing the SiO2 content to increase the durability of cements [3]. Our study also confirmed a strong positive correlation (r = 0.87) between SiO2 and sulfate resistance.
The correlation analysis results show significant correlations between the component composition of MCCs and their properties. In particular, a study by M. Thomas et al. (2021) notes that the use of thermal activation of slags leads to an improvement in strength characteristics [6]. This coincides with the data obtained, where thermally activated slags showed an increase in strength by 12–15%, compared with non-activated ones [1]. Thermal activation increases the reactivity of components. According to literature data, thermal activation increases the degree of hydration of slags, which leads to the formation of a stronger cement matrix [25]. Let us make a calculation based on the composition and correlation analysis. To assess the effect of thermal activation on strength, we use the strength gain formula:
(4)
where σactive — strength of cement with thermally-activated slags; σinactive — strength of cement with inactive slags.
According to the correlation analysis results, formula (3) takes the form:
(5)
Thus, if the base strength of cement (σinactive) is, for example, 30 MPa, then the change will be as follows:
This corresponds to the literature data and confirms the correlation presented in the study. Optimal activation of additives, for example, blast furnace slag, leads to an increase in strength by 12−15%, which is consistent with the specified coefficient.
A study by A.M. Rashad (2023) shows that the addition of CaO to the cement matrix increases strength in the early stages of hardening, but reduces resistance to sulfate attacks [1]. Our data confirm this: the correlation between CaO and sulfate resistance is only r = 0.28. At the same time, the use of additives rich in aluminates leads to improved resistance in aggressive environments.
An unexpected result was the negative effect of the silicate blast furnace additive on sulfate resistance. This requires further investigation and may be due to the presence of impurities in the slag or the specifics of its interaction with other cement components. The work of M.R. Sakr and M.T. Bassuoni (2021) discusses impurities (MgO, K2O) in slags, which can reduce the stability of cements [4]. This is consistent with the assumption of a possible influence of slag composition in our study. The effect of C3A content on sulfate resistance also requires additional research, as there are conflicting data in the literature and standards from different countries.
The correlation between self-tension and sulfate resistance (r = 0.97) highlights the importance of the material's internal resistance to aggressive media. The result complements the known data presented in the article by I.P. Pavlova and K.Yu. Belomesova (2021), in which self-tension is associated with increased strength and durability [30].
The relationship of linear expansion with the SiO2 content (r = 0.88) confirms that silica plays a key role in controlling the volume changes of cement. However, the MCC composition shows different behavior when using hydrogranates, which is due to their different crystal structure. This opens up new perspectives for studying the interactions between the components and the possibilities of optimizing the composition to achieve the required characteristics.
Thus, the results of the study fill in the gaps in knowledge about the effect of the composition of MCCs on their properties and provide mathematically sound recommendations for improving environmental and economic efficiency.
Statistical processing of experimental data confirmed the significant effect of MCCs composition on their operational characteristics, including sulfate resistance, linear expansion and self-tension. The correlation analysis carried out in the framework of the study revealed a strong relationship between the SiO2 content and sulfate resistance, as well as between self-tension and sulfate resistance, which is important for the development of environmentally effective formulations. An increase in the proportion of SiO2 by 1% provides an increase in sulfate resistance by 0.5 units, which is consistent with calculations and data from literary sources and confirms the key role of SiO2 in managing cement properties.
Statistical evaluation shows that reducing the proportion of clinker and replacing it with alternative materials such as slags and phosphogypsum improves the environmental performance of the MCC by reducing CO2 emissions and reducing cost. Calculations based on the experimental data confirmed a 46.2% reduction in CO2 emissions when replacing a part of the clinker, which corresponds to the sustainable development goals. The economic effect of replacing clinker with additives is expressed in reducing the cost of cement production by 10–15% due to the use of waste. This result is consistent with the data from the literature and highlights the environmental importance of using industrial wasteа.
The analysis carried out by the author confirmed the significant influence of the MCCs chemical composition on their operational characteristics. It was found that reducing the clinker content by 30% and replacing it with activated additives such as blast furnace slags and phosphogypsum could reduce the carbon footprint by 25–40%.
The use of thermal activation of slags has shown an increase in the strength characteristics of cements
by 12–15%. This is due to the improved reactivity of the activated components, which contributes to the formation of a more dense and durable cement matrix. Further research is needed to clarify the optimal temperatures and conditions of thermal activation.
The effect of hydrogarnets on the properties of cements revealed their complex behavior due to their crystalline structure. It has been established that changes in the content of hydrogarnets affect linear expansion and self-tension, which opens up prospects for the creation of materials with specified characteristics. This area requires additional research for an in-depth study of the mechanisms of interaction of the components.
The results obtained during statistical processing, in particular the negative correlation between silicate blast furnace additive and sulfate resistance, indicate the need for further research. A more detailed statistical analysis of the influence of impurities in the slag, the content of C3A and other factors on the sulfate resistance and properties of MCCs is required to develop optimal environmentally friendly formulations.
1. GOST 310.1.76. Cements. Test Methods. General. (In Russ.) URL: https://internet-law.ru/gosts/gost/34404/?ysclid=m9hv0dql9976146066 (accessed: 13.01.2025).
2. GOST 310.4–81. Cements. Мethods of Bending and Compression Strength Determination. (In Russ.) URL: https://internet-law.ru/gosts/gost/13713/ (accessed: 13.01.2025).
3. TU 21–26–13–90. Self-Stressing Cements. Unupdated Version. (In Russ.) URL: https://nd.gostinfo.ru/document/3203787.aspx (accessed: 13.01.2025). Current GOST R 56727–2015. Self-Stressing Cements. Specifications. (In Russ.) URL: https://files.stroyinf.ru/Data2/1/4293758/4293758145.pdf (accessed: 13.01.2025).
4. GOST 31108–2020 Common Cements. Specifications. (In Russ.) URL: https://internet-law.ru/gosts/gost/73873/?ysclid=m9iwx3cpwg983001164 (accessed: 13.01.2025).
5. Yezhov VB. Technology of Concrete, Building Products and Structures. Manual. Yekaterinburg: Ural Federal University named after the first President of Russia B.N. Yeltsin; 2014. 206 p. (In Russ.) URL: https://study.urfu.ru/Aid/Publication/12435/1/Ejov_2.pdf (accessed: 13.01.2025).
References
1. Rashad AM. A Concise on the Effect of Calcium Oxide on the Properties of Alkali-Activated Materials: A Manual for Civil Engineers. International Journal of Concrete Structures and Materials. 2023;17(1):72. https://doi.org/10.1186/s40069-023-00635-y
2. Rashad AM. Effect of Steel Fibers on Geopolymer Properties – The Best Synopsis for Civil Engineer. Construction and Building Materials. 2020;246:118534. https://doi.org/10.1016/j.conbuildmat.2020.118534
3. Rahman MM, Bassuoni MT. Thaumasite Sulfate Attack on Concrete: Mechanisms, Influential Factors and Mitigation. Construction and Building Materials. 2014;73:652–662. https://doi.org/10.1016/j.conbuildmat.2014.09.034
4. Sakr MR, Bassuoni MT. Effect of Nano-Based Coatings on Concrete under Aggravated Exposures. Journal of Materials in Civil Engineering. 2020;32(10):04020284. https://doi.org/10.1061/(asce)mt.1943-5533.0003349
5. Sivkov SP. A New Standard for Sulfate-Resistant Cement: Recommendations for Producers and Consumers. Cement and Its Applications. 2015;(1):56–58. (In Russ.)
6. Thomas M, Folliard K, Drimalas T, Ramlochan T. Diagnosing Delayed Ettringite Formation in Concrete Structures. Cement and Concrete Research. 2008;38(6):841–847. https://doi.org/10.1016/j.cemconres.2008.01.003
7. Paulava I. Superplastisizers Influence on Expansive Cementitious Systems Properties. Vestnik of Polotsk State University. Part F. Constructions. Applied Sciences. 2016;(16):35–40. (In Russ.)
8. Markiv T, Sobol K, Petrovska N, Hunyak O. The Effect of Porous Pozzolanic Polydisperse Mineral Components on Properties of Concrete. Lecture Notes in Civil Engineering. 2020;47:275–282. https://doi.org/10.1007/978-3-030-27011-7_35
9. Srikakulam LM, Khed VC. Theoretical Research and Performance of Engineered Cementitious Composite. Springer Proceedings in Materials. 2020;8:253–264. https://doi.org/10.1007/978-981-15-7827-4_25
10. Woo Sung Yum, Jung-Il Suh, Dongho Jeon, Jae Eun Oh. Strength Enhancement of CaO-Activated Slag System through Addition of Calcium Formate as a New Auxiliary Activator. Cement and Concrete Composites. 2020;109:103572. https://doi.org/10.1016/j.cemconcomp.2020.103572
11. Sanytsky M, Marushchak U, Olevych Y, Novytskyi Y. Nano-Modified Ultra-Rapid Hardening Portland Cement Compositions for High Strength Concretes. Lecture Notes in Civil Engineering. 2020;47:392–399. https://doi.org/10.1007/978-3-030-27011-7_50
12. Shakhova LD, Kucherov DE. Features of the Behavior of Multicomponent Cements in Concrete. Bulletin of Belgorod State Technological University Named after. V.G. Shukhov. 2008;(3):27–29. (In Russ.)
13. Chomaev MN. Ecology of Cement Production. International Journal of Humanities and Natural Sciences. 2019;2–1:8–10. (In Russ.) https://doi.org/10.24411/2500-1000-2019-10522
14. Khokhryakov OV. Composite Cements of Low Water Consumption and Building Materials Based on Them. Dr. Sci. (Eng.) diss. Kazan; 2022. 460 p. (In Russ.)
15. Khozin VG, Khokhryakov OV, Sibgatullin IR, Gizzatullin AR, Kharchenko IYa. Carbonate Cements of Low Water-Need Is a Green Alternative for Cement Industry of Russia. Construction Materials. 2014;(5):76–82. (In Russ.)
16. Puzatova AV, Dmitrieva MA, Leitsin VN. Evaluation of the Efficiency of Mechanical Activation of the Initial Components of a Cement-Based Composite Material. Far Eastern Federal University: School of Engineering Bulletin. 2024;4(61):3–17. (In Russ.) https://doi.org/10.24866/2227-6858/2024-4/3-17
17. Dykin IV. Powder-Activated Concretes — Multilevel-Modified Concrete Systems. International Research Journal. 2017;3–4(57):37–40. (In Russ.) https://doi.org/10.23670/IRJ.2017.57.121
18. Schnabel M, Buhr A, Dutton J. Rheologie of High Performance Alumina and Spinel Castables. New Refractories. 2017;(3):119–126. (In Russ.) https://doi.org/10.17073/1683-4518-2017-3-119-126
19. Yudovich BE, Dmitriev AM, Lyaminyan YuA., Zubekhin SA. Cement Industry and Ecology. Cement and Its Applications. 1998;(3):11–19. (In Russ.)
20. Shilin Yang, Bieliatynskyi A., Trachevskyi V., Meiyu Shao, Mingyang Ta. Research of Nano-Modified Plain Cement Concrete Mixtures and Cement-Based Concrete. International Journal of Concrete Structures and Materials. 2023;17:50. https://doi.org/10.1186/s40069-023-00601-8
21. Sydor N, Marushchak U, Braichenko S, Rusyn B. Development of Component Composition of Engineered Cementitious Composites. Lecture Notes in Civil Engineering. 2021;100:459–465. https://doi.org/10.1007/978-3-030-57340-9_56
22. Andreev VV, Smirnova EE. Cement. RF Patent, No 2079458. 6 p. (In Russ.) URL https://patents.s3.yandex.net/RU2079458C1_19970520.pdf (accessed: 14.02.2025).
23. Brykov AS. Sulfate Corrosion of Portland Cement Concretes. Cement and Its Applications. 2014;(6):96–103. (In Russ.)
24. Potapov VV, Gorev DS, Cerdan AA. Physical and Chemical Characteristics Ofnanosilica and Microsilica SiO2. Eastern European Scientific Journal. 2023;5–2(90):26–33. (In Russ.) https://doi.org/10.31618/ESSA.2782-1994.2023.2.90.370
25. Han-Seung Lee, Xiao-Yong Wang, Li-Na Zhang, Kyung-Taek Koh. Analysis of the Optimum Usage of Slag for the Compressive Strength of Concrete. Materials. 2015;8(3):1213–1229. https://doi.org/10.3390/ma8031213
26. Juan He, Shuya Yu, Guochen Sang, Junhong He, Jie Wang, Zheng Chen. Properties of Alkali-Activated Slag Cement Activated by Weakly Alkaline Activator. Materials. 2023;16(10):3871. https://doi.org/10.37614/2949-1185.2022.1.2.007
27. Bikbau MJa, Bikbau JaM, Chehn' L. Method of Production of Cement Clinker. RF Patent, No. 2342337. 2007. (In Russ.)
28. Bastrygina SV, Konokhov RV. Influence of Silica-Containing Additives on Strength Properties of Lightweight Concrete on Porous Aggregate. Transactions of the Kola Science Centre of RAS. Series: Natural Sciences and Humanities. 2022;1(2):58–66. (In Russ.) https://doi.org/10.37614/2949-1185.2022.1.2.007
29. Dzhabbarova NE, Gasanova UF. The Effect of Silica Additives on Concrete Strength. Problems of Science. 2022;1(69):12–15. (In Russ.)
30. Paulava I, Belamesava K. Influence of Disperse Reinforcement on the Strength Properties of Expansive Cement Binders with High Expansion Energy. In: Architectural and Construction Complex: Problems, Prospects, Innovations: Electronic Collection of Articles of the III International Scientific Conference. Novopolotsk, 2021. Novopolotsk; 2021. P. 111–118. (In Russ.)
About the Author
E. E. SmirnovaRussian Federation
Elena E. Smirnova, Cand. Sci. (Eng.), Associate Professor of the Department of Industrial Ecology
14, Professora Popova St., lit. A, St. Petersburg, 197376
Review
For citations:
Smirnova E.E. Assessment and Prediction of the Environmental Performance of Multi-Component Cements Using Statistical Analysis. Safety of Technogenic and Natural Systems. 2025;(2):87-101. https://doi.org/10.23947/2541-9129-2025-9-2-87-101. EDN: GJCTOU